Casting the Real McCoy
Silver Bullet Pages | |
---|---|
|
|
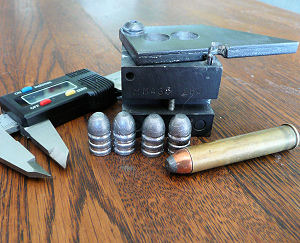
I spent the better part of a day machining a dozen or so sprue-plate insulators for the new mold, then arranged to meet Dr. Jaansalu in the labs. We gave the sprue-plate insulators the benefit of another hour or so at 450°C just to make sure they were really dry then began trying to cast some useable silver bullets.
Naturally, things didn't go as smoothly as we had hoped. It turns out that the sprue-holes I had machined were ever-so-slightly too small, and the plates may have been a little thick. The casts looked good, but there were obvious voids in several of the bullets, particularly near the base. The results weren't terrible, but they weren't as consistent as I would have liked. In the end, only about half of the bullets were useable, and even those weren't as dimensionally-consistent as I had hoped.
We also found that, with smaller bullets, a disconcertingly high percentage of the silver ended up as casting waste and flashings. I ran out of silver long before I ran out of insulators. Given the inconsistency of our current casting method, building a box of bullets is likely to be a slow and expensive. I'm hoping that changing the insulator design a little, and possibly using a hot-plate to keep the mold warm will yield more predictable results. On the other hand, ignoring the failures and difficulties, I can finally hold in my hand a few very real silver bullets, and they look good. The following photo shows the mold with a mix of silver and lead bullets; can you see the difference? Notice the two silver bullets still in the mold.

Cold Hard Numbers
The most pressing question is how these bullets measure up. I picked a half-dozen of the best-looking bullets, grabbed my micrometer, and took some measurements. I don't yet have the weights, but I'll try to get those in the near future. As expected, the first thing that jumps out is that the silver bullets are far more variable than the lead bullets cast from the same mold. However, the very best castings are perfectly sized, and presumably deadly.
Diameter (in) | Length (in) | Weight(g) | ||||
---|---|---|---|---|---|---|
Sample | Lead | Silver | Lead | Silver | Lead | Silver |
1 | .4335 | .4275 | .7680 | .7660 | ||
2 | .4350 | .4320 | .7675 | .7550 | ||
3 | .4350 | .4220 | .7665 | .7640 | ||
4 | .4340 | .4260 | .7675 | .7660 | ||
5 | .4345 | .4290 | .7680 | .7630 | ||
6 | .4340 | .4310 | .7670 | .7600 | ||
Average: | .434 | .428 | .767 | .762 | ||
Difference: | -1.48% | -0.66% |
Final Thoughts on Casting
OK, since writing the above, I've gone back and cast a number of additional bullets. I've made some minor tweaks to the sprue plate design (and you can find complete details on building them later in this article). I have discovered a couple of "tricks" that make a huge difference.
First, silver has a diconcerting propensity to pick up dissolved oxygen. When you pour it, the oxygen is realeased with a sizzle at the instant the silver freezes, creating little voids and possibly throwing molten silver out of the mold. When melting the silver, add a few lengths of graphite rod to the furnace, and put at least one in the crucible with the silver. The graphite burns readily, and consumes the free oxygen in the furnace before it can dissolve into the silver.
Second, the release agent makes a world of difference in the appearance of the final bullet. I've gone back and forth between carbon (soot) and Boron Nitride. With no relase agent (bare mold) the silver doesn't stick to the mold as feared, but it fails to conform to the mold cavity perfectly. Similar to the surface tension in water, the silver shows high cohesion and tends to pull back from contact with the mold, resulting in a badly wrinkled bullet (and a high probability of voids and other problems).
Boron Nitride acts as a wetting agent - reducing the surface tension and giving a very smooth, beautiful finish to the cast bullet. For jewelry, this would be the clear winner. However, the the driving bands tend to be incompletely filled, the edges slightly rounded rather than showing crisp, sharp angles. I'm not sure whether this is due to the Boron Nitride actually filling the mold, or some chemical property.
Carbon (applied by holding the mold over a sooty flame) is probably the best release agent for functional bullets. The resultant bullets show very crisp, clean casting on the driving bands, and considerably less wrinkling than with an uncoated mold. They're not quite as pretty looking as those cast using Boron Nitride, but I don't necessarily need pretty. The problem with the carbon coating is that it needs to be re-applied frequently, and it's easier to get the carbon to stick to a cold mold than a hot one. I tend to get a few really nice casts, then run into problems as the mold heats up.
Despite my best efforts, casting remains less than perfectly predictable. I end up with about 75% of my bullets being useable, and maybe half looking good. This is a slow and expensive way to produce bullets.
Next: Sprue Plate Insulators